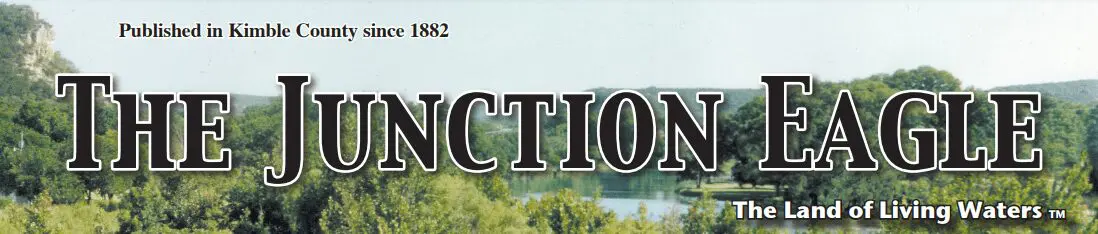
Published in Kimble County Since 1882
Sharing Local News and Features
Published in
Kimble County
Since 1882
Sharing Local News and Features
The Leading Community-Focused News Source
The Junction Eagle offers a community-minded newspaper. We have been providing relevant local news to residents in Junction, Texas and surrounding counties for more than 140 years.
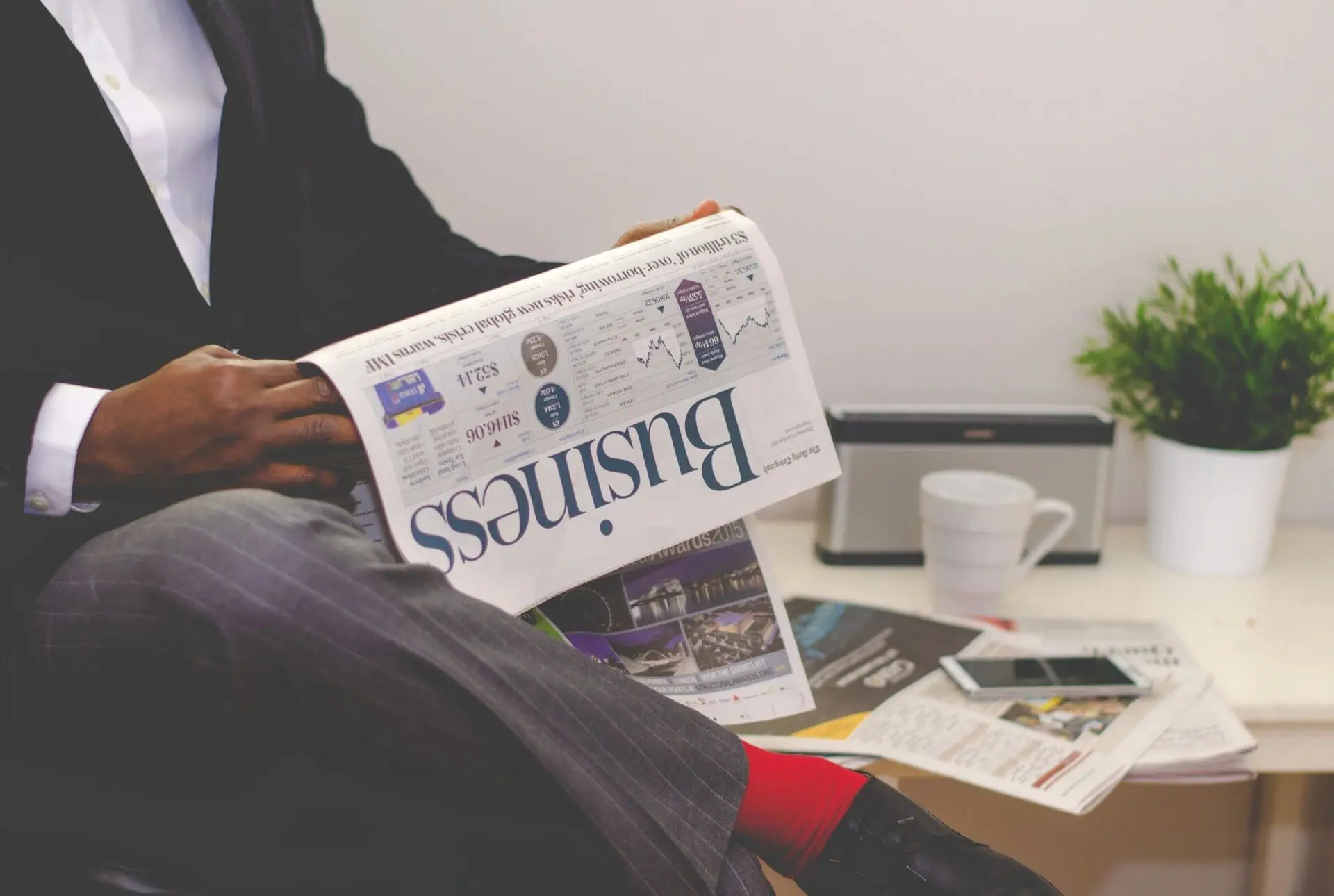
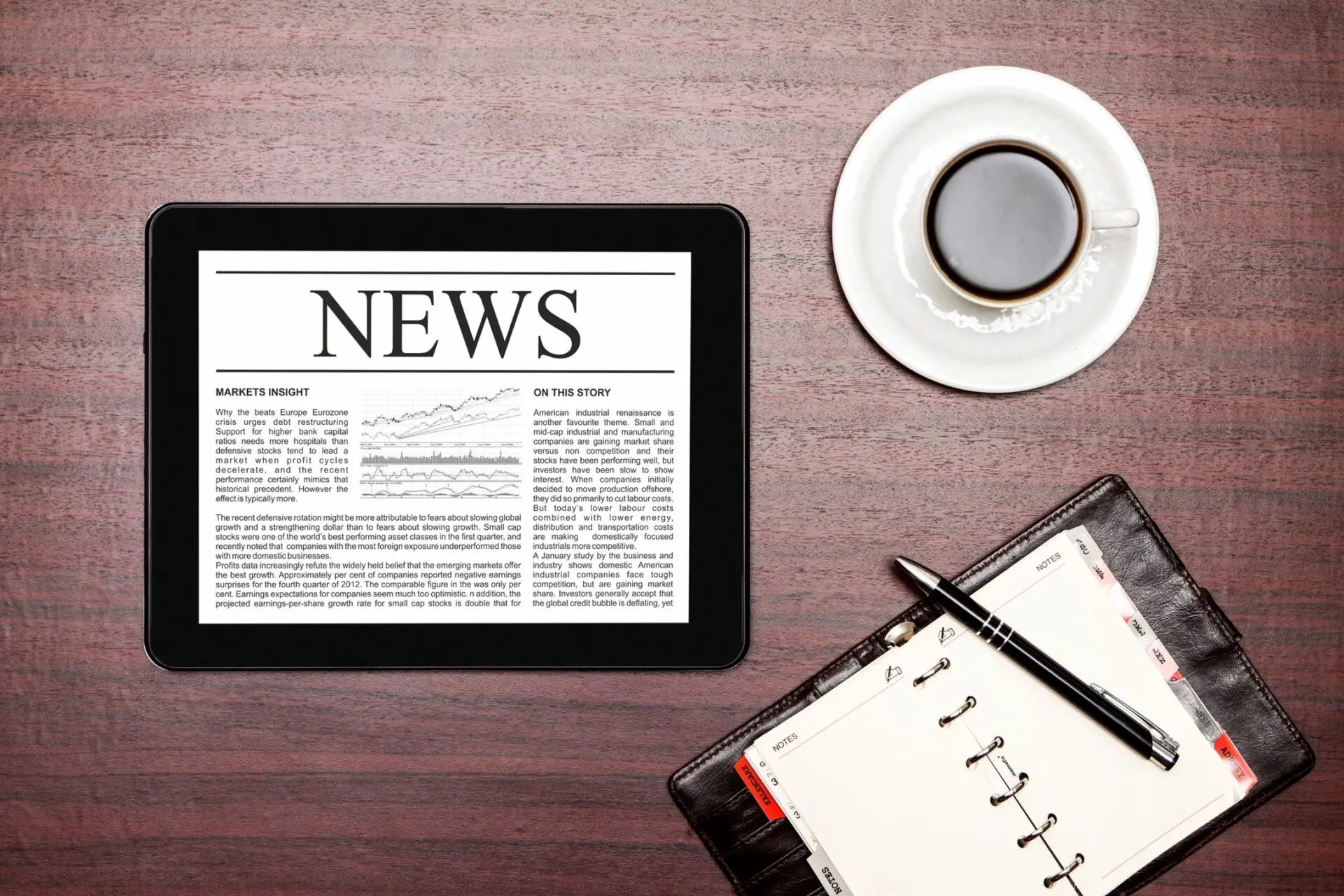
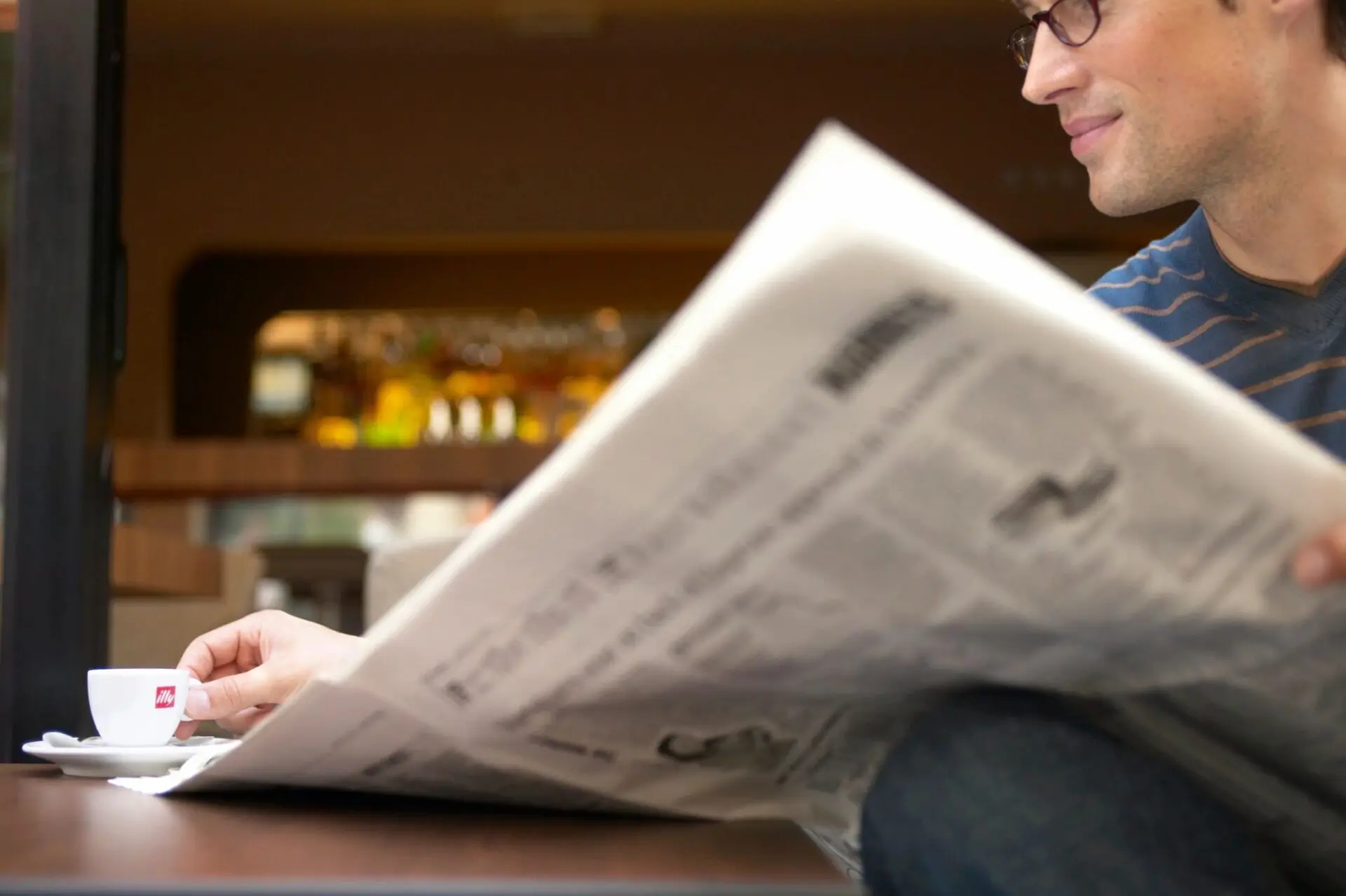